Mining in the Amazon: investments under safety and sustainability
With a large concentration of mining activities, the state of Pará accounts for almost 50% of Brazilian mineral production. Companies operating in the region seek to innovate using technologies to reduce risks, address environmental issues and increase operational safety

Mineral production in the Amazon requires additional care and investment. Besides the issues involving logistics and access, which pose greater challenges compared to other regions of the planet where this activity is carried out, mineral extraction in the Amazon demands that sustainability and safety in industrial processes become almost a ‘mantra’, turning into the focus of internal investments by companies that seek innovation and technology to ensure best practices. On top of the obvious gains, this attitude of environmental responsibility is also an important message to the market, which always calls for respect towards nature, especially in the Amazon.
Currently, Pará concentrates most of the mineral production in the Brazilian Amazon, accounting for 49.2% of total national production, according to data from the Anuário Mineral Brasileiro 2020 [Brazilian Mineral Yearbook], produced by Agência Nacional de Mineração (ANM) [National Mining Agency]. The second main producer is Minas Gerais, which concentrates 40.1% of national production. Among the other states from the Brazilian Legal Amazon with mineral production, are Mato Grosso, with a 1.85% share; Amapá, with 0.60%; Rondônia, with 0.38%; Maranhão, with 0.34% and Amazonas, with 0.33%.
In Pará, the mining sector recovered higher growth rates in 2021. In line with data from Instituto Brasileiro de Mineração (IBRAM) [Brazilian Mining Institute], Pará registered an increase of 119% in sales, that is, from 21.6 billion dollars in the third quarter of 2020 to $47.2 billion in the third quarter of this year. Within the current year, the increase represented 38% compared to the second quarter. To keep this pace, the sector should continue investing in the coming years.
Sector requires investment in operational safety
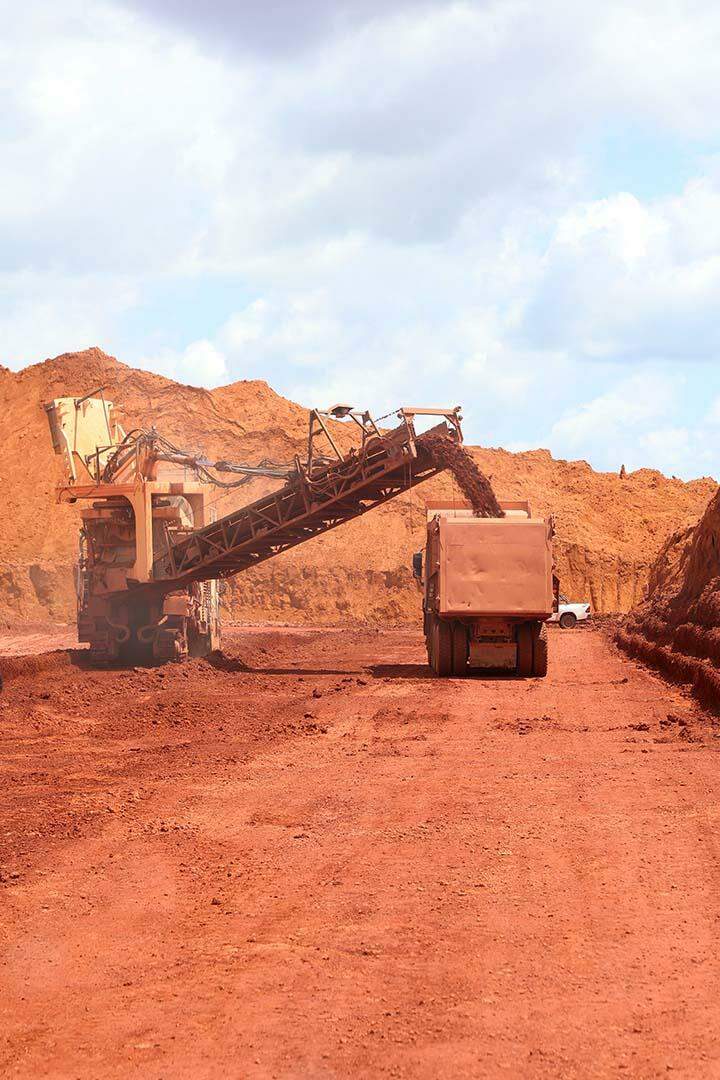
IBRAM estimates that the country will register around US$ 41.3 billion in investments in the sector by 2025. Funds will be destined, mainly, to socio-environmental projects, but also to innovation and technology that ensure greater sustainability, safety and protection to the sector, especially in the operational security of activities, for employees, environment and populations.
At this point, the issue of dams represents a common concern among companies operating in the region marked by the inherent characteristic of the tropical and humid forest - the heavy rains.
Currently, there are 907 mining dams in Brazil, according to data from Agência Nacional de Mineração (ANM) [National Mining Agency], which carries out frequent inspections. The agency's bulletin of November 2021, reports that 335 of these dams are located in the nine states that compose the Legal Amazon: 142 in Mato Grosso, 114 in Pará, 36 in Rondônia, 18 in Amapá, 15 in Amazonas, 7 in Tocantins and 3 in Maranhão.
Dams are constructions that contain and accumulate large amounts of water, as well as other liquid and solid materials. Marcelo Rassy Teixeira, associate professor at the Federal University of Pará (UFPA), PhD in Civil Engineering and post-doctorate in Geology and Geochemistry, explains that large dams hold some differences among them, such as hydroelectric structures and types. Tailings dams, for example, accumulate residues from industrial processes, as in the case of mining companies.
Accidental collapse of dams – in the cities of Mariana and Brumadinho, both in Minas Gerais – were disastrous warnings about the importance of keeping inspection activities. As stated by the engineer, similar accidents are unlikely to happen in the Amazon region and the use of technology is crucial to avoid damages, whether human, environmental or structural. " The failure of hydroelectric dams is something more likely to cause damage, however, they are structures with a high degree of reliability and frequent maintenance. In my opinion, accidents like these are improbable in the region. And the importance of technology for safety and effectiveness of activities is certainly involved", he says.
Technology allows tailings to return to mined areas
In Pará – where the largest mineral production in the country is concentrated – there is an effort on the part of large companies operating in the region towards advancing in safer and more sustainable practices. The city of Paragominas, located just over 300 kilometers from Belém [the capital of Pará], was the place chosen to implement a pioneering solution when it comes to technology and dams: a methodology that allows tailings from bauxite mining to be relocated in areas that are already open and mined, thus speeding up the process of rehabilitation of sites that have already been explored. This proceeding fosters the progress of the reforestation project carried out by Mineração Paragominas, where Hydro's bauxite mine is based.
After going through the plant, there are two outcomes. One is the product, which is basically bauxite ground with water – we call it ‘pulp’ – destined to be pumped to the customer. (...) And we also have tailings – ‘silica’, a contaminant that is not good for aluminum production" - Victor Silva, a process control supervisor
The entire process is monitored by a specialized center set up inside the mine, in charge of controlling everything that happens, from extraction to transportation through a pipeline (which also receives systematic maintenance). From this center, it is possible to provide guidance to employees working in the field, 24 hours a day, seven days a week, preventing accidents and ensuring a more effective work performance in the mine.
Victor Silva, a process control supervisor, explains that the pipeline runs for 244 kilometers and crosses seven municipalities in Pará, transporting the extracted ore to the headquarters of the largest alumina refinery in the world outside China – Alunorte, in Barcarena. "The process starts in the mine site, where the ore is extracted and removed in trucks until the next stage – the beneficiation plant. The product that leaves the mine, at this point, is still not ready to be delivered to our client and that is why it needs to go through the plant phase for both chemical and physical adjustments. This material is still very coarse, so you have to grind it until it becomes thinner and able to be pumped to the customer," he details.
Once extracted from the mine, the material needs to undergo a kind of initial "sieve", when water is added to separate the bauxite from the silica, the sand that is mixed with the earth where the product is found. "After going through the plant, there are two outcomes. One is the product, which is basically bauxite ground with water – we call it ‘pulp’ – destined to be pumped to the customer. (...) And we also have tailings – ‘silica’, a contaminant that is not good for aluminum production", he adds.
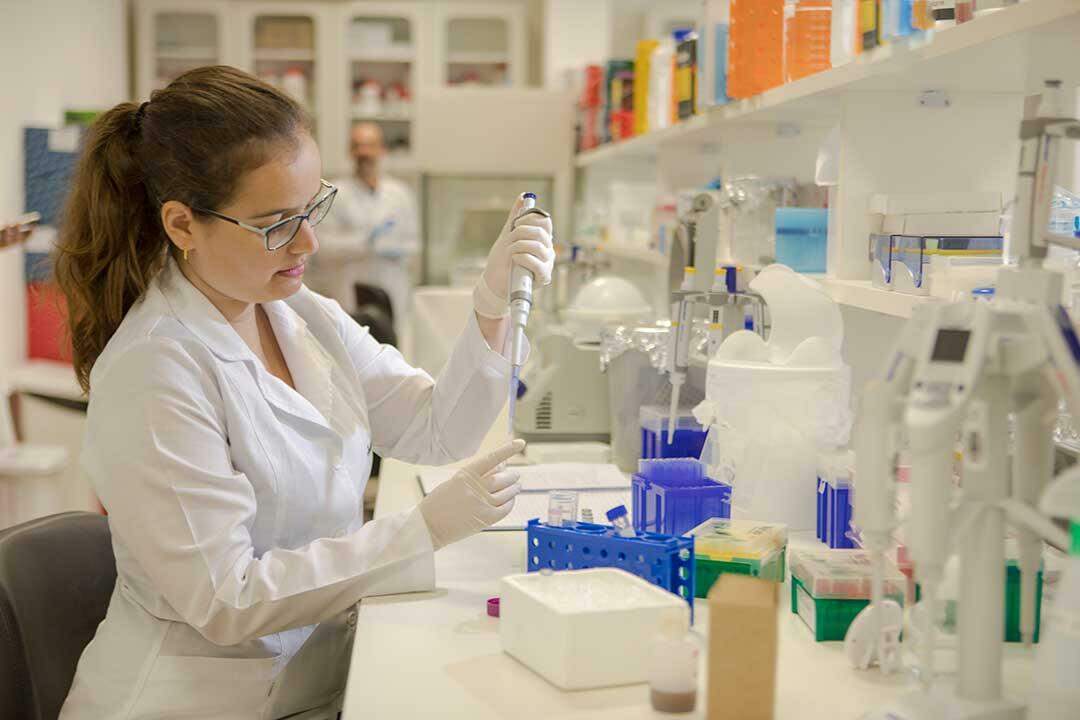
To handle this production “leftover”, Mineração Paragominas has two dam systems for storing bauxite tailings. Both systems employ a methodology based on the alternating operation of reservoirs, allowing the material to dry, combining drainage and evaporation and resulting in tailings with a minimum content of 60% solid. This procedure reduces, even more, the already minor risks of landslides in the region, leaving a firm ground, even for those who want to walk on it.
The major technological difference of this method known as “Tailings Dry Backfill” is precisely the waste releasing system. It replaces the idea of simply liberating the tailings in the same area, thus resulting in dam areas formed by means of an almost self-regulatory process, which re-uses the waste to restore previously mined areas.
Evilmar Fonseca, the industrial director of Hydro Paragominas company, details … “This method considerably reduces any investments related to the dam. Formerly it would have a structure of 30 meters, a lot of other structures that would take up some space corresponding to 1,800 hectares. Now, this unused area is reduced. This kind of method allows us to use only 400 hectares. Besides that, the height level does not need to be increased. The process is much easier, safer to the people, to the operation and to the environment”.
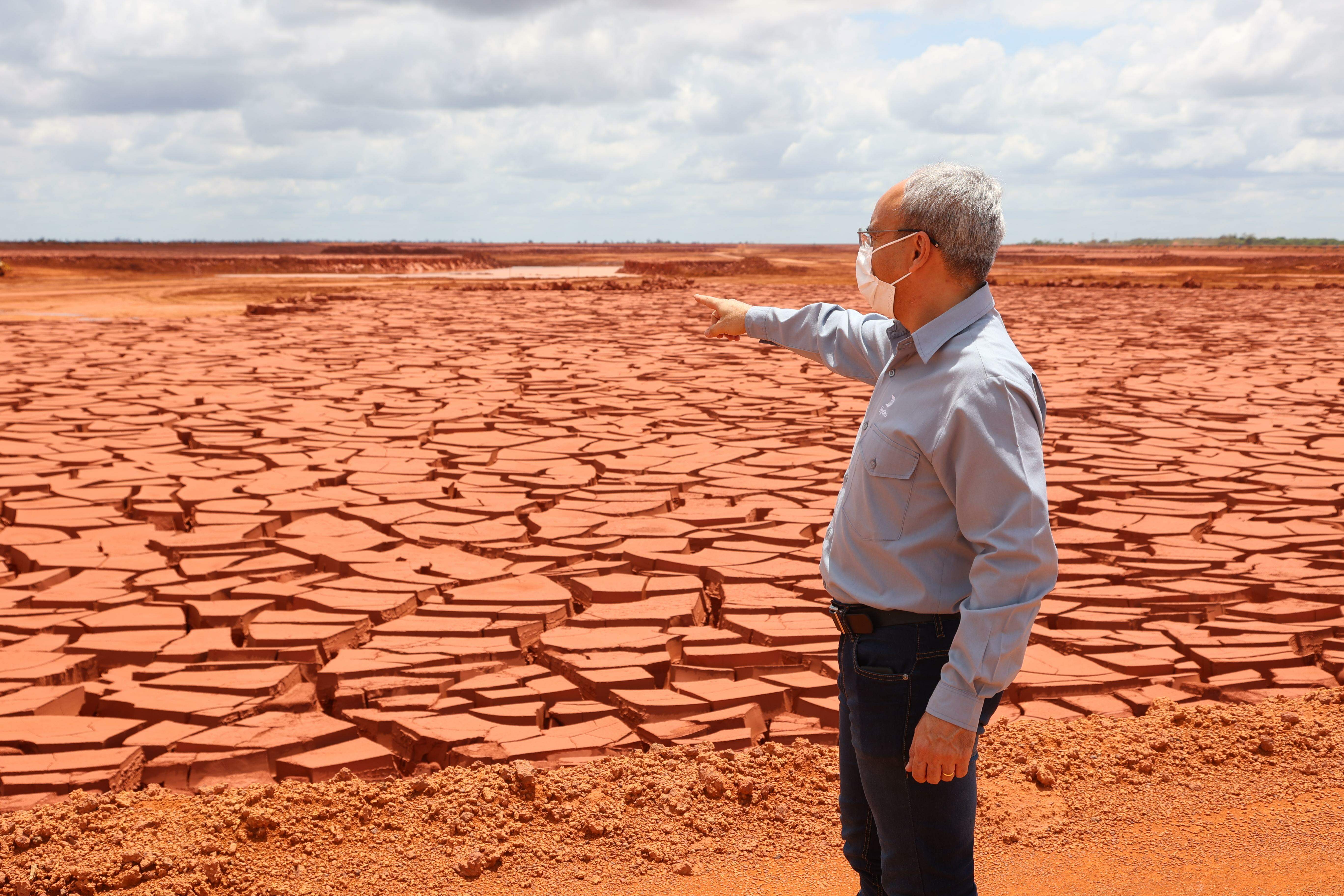
In addition to reducing risks to employees and workers, the impact to the environment is another benefit of that technology, since all the area used for mining is reforested after three years. “I think the main impact of this project is the awareness of not building more dams and recovering the environment. All the tailings get back to their original place. Before the project, the environmental recovery of such dam area would only occur after 30,40, or even 50 years”, he evaluates.
Model applied in Paragominas is replicated in other areas.
The “Tailings Dry Backfill” methodology seems to point to a new path in the mining field. So much that the project copyrighted by Hydro company has started to be applied by Mineração Rio do Norte company (MRN), for bauxite extraction in the city of Oriximiná, in the west of Pará. Instead of using dams, the company has also implemented the tailings management system. The waste is released in 24 storage tank units, as a way to reduce the risks of collapsing, by storing the gangue left after mineral processing.
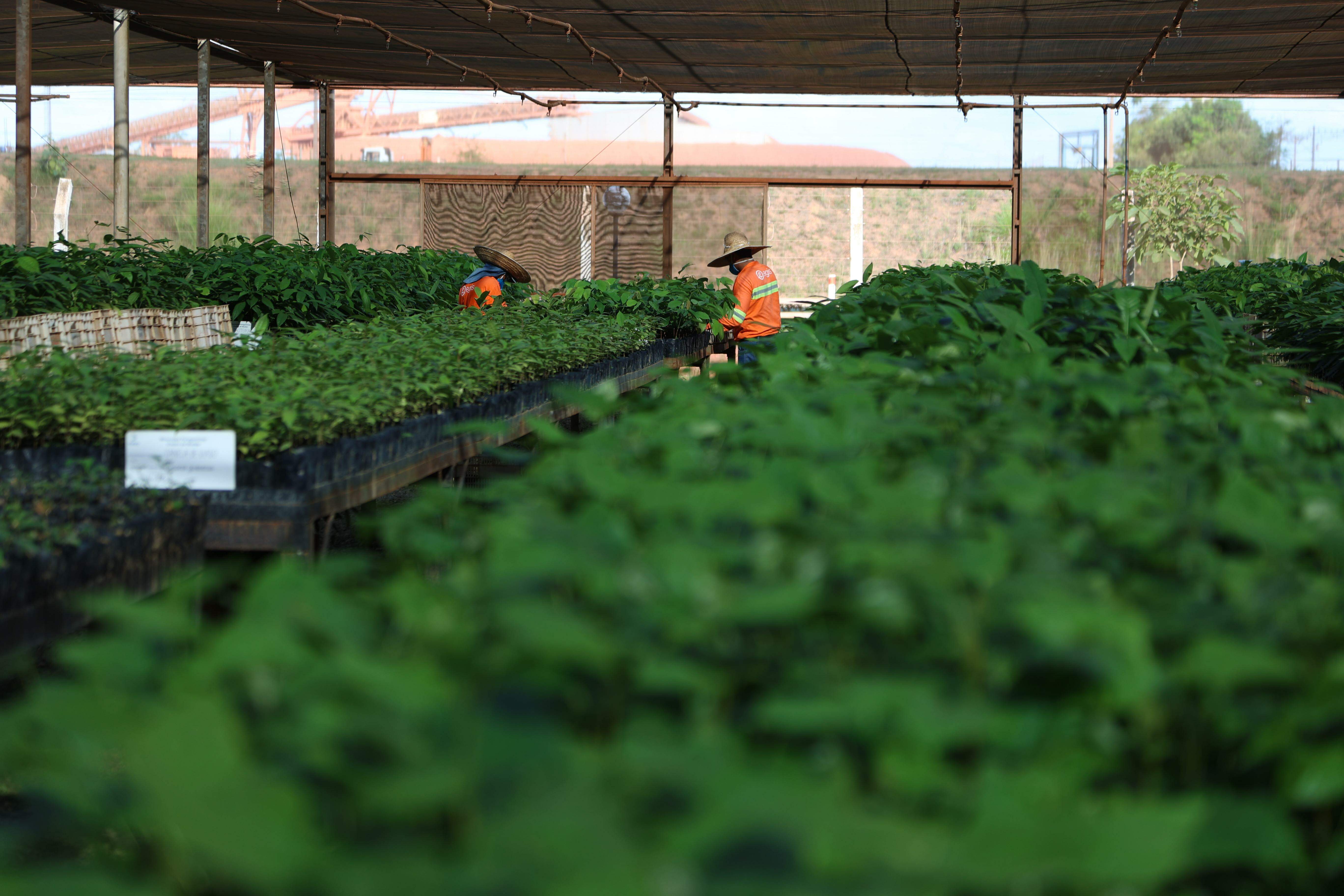
Mining extraction that uses dam method releases waste with a large amount of water, differently, in “Tailings Dry Backfill” system the waste is dumped in storage facilities, which are built in a total area of approximately 1,500 hectares, after re-using almost 80% of the liquid part in other processes. The waste left (around 20%), penetrates the ground or evaporates naturally, within a period of 30 to 60 days.
Currently, the mining company has two dams to store and treat the rainwater. For those structures, despite the low risk of collapses, there are standard procedures, called Plano de Ações Emergenciais para Barragens de Mineração (PAEBM) [Emergency Action Plan of Mining Dams]. A team of almost 70 professionals manages the operation activities and safety inspection of the tailings system, guided and supervised by national and international companies, employing inspecting and procedural routines, maintenance and prevention. The constant elaboration of inspection analysis and monitoring reports also reaffirms the low risk of collapses in the mine area.
One of the major solutions that makes the S11D production a reference in terms of environmental aspects is that it gathers almost 80 years of expertise in mining and a system composed by excavators and mobile crushers, connected by conveyor belts. That kind of system reduces the emission of polluting gases and the mineral processing is done without using water, thus, without the necessity of building tailings dams, due to the high-quality iron mineral that exists here” - Antônio Sérgio, Executive Manager of the Serra Sul Mine (S11D).
During the summer season, the tailings storage is done in layers of 50 centimeters, so after 30 days, it is possible to deposit another layer, however, during winter season, the layers timing goes up to 60 days. The different layering times assure safety.
Alexandre Schuler, manager of the Geotechnics Department at MRN [Mineração Rio do Norte Company], explains that 1,100 sensors monitor the water pressure, operating around the clock. Most part of its operations are automated. Data collected are sent to the monitoring room. “At the slightest sign of any error, we head to the site and contact the consulting professionals to ask if it is something we should worry about. There are inspections carried out by technicians full time. They work exclusively on that”, he highlights.
Mineral extraction in Canaã no longer uses dams.
The investment in technology and in protection actions, known as “Mosaico de Carajás” [Carajás Mosaic], an area where the Vale mining company operates in Pará, is one of the flagships of the company, which has operated in the Amazon region for 30 years. The area, corresponding to five times that of the city of São Paulo, is responsible for 60% of the iron mineral production and extraction by the multinational corporation. The area also shelters the largest open air iron mineral mine in the world.
Besides mineral extraction, the 800 thousand hectar area also comprises six preservation units: Floresta Nacional (Flonaca), Reserva Biológica do Tapirapé, Floresta Nacional do Tapirapé-aquiri, Floresta Nacional do Itacaiúnas, Área de Proteção Ambiental do Igarapé Gelado and Parque Nacional dos Campos Ferruginosos (Parna). However, according to the company, the actions carried out by Vale affect only 2% of the area. The region under the company’s responsibility has become a kind of “green oasis” in the midst of the Amazon forest. The increase of different exploratory activities has aggravated the deforestation in the region, but the “mosaic” remains untouched – and green, as shown in the images provided by the satellites and monitored by the company for decades.

During the last decade, the company has invested more than R$ 1 billion Reais in actions for environmental preservation, research, development in the region and culture fostering projects. R$ 910 million of that budget were voluntary contribution.
In that scenario, an outstanding project is the S11D Complex, which conciliates economic activities and environmental preservation. In the iron mining site, located in the municipality of Canaã dos Carajás - Southeast of Pará – the mineral is processed in a plant outside the forest area and the ore processing uses a totally water-free system, eliminating the need to use water or dams. This procedure prevents the production of liquid tailings and the necessity of risk management to the workers and to the community.
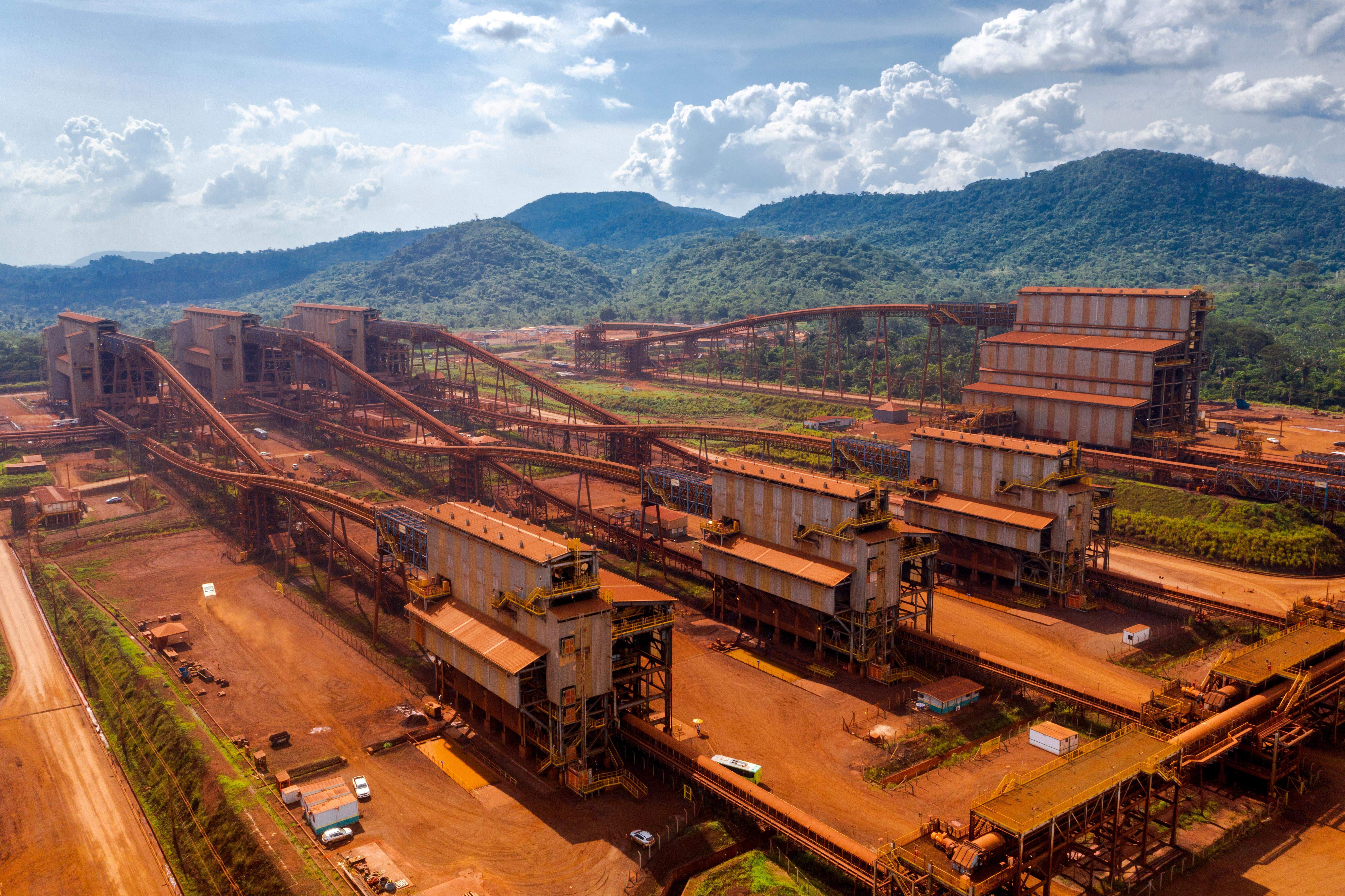
“One of the major solutions that makes the S11D production a reference in terms of environmental aspects is that it gathers almost 80 years of expertise in mining and a system composed by excavators and mobile crushers, connected by conveyor belts. That kind of system reduces the emission of polluting gases and the mineral processing is done without using water, thus, without the necessity of building tailings dams, due to the high-quality iron mineral that exists here”, highlights the Executive Manager of the Serra Sul Mine (S11D), Antônio Sérgio.
In addition to the innovative solutions, investments in forest safety, sponsoring forest guard teams to support the Instituto Chico Mendes de Conservação da Biodiversidade (ICMBio) [Chico Mendes Institute of Biodiversity preserving], have made it possible to carry out 9,835 patrols on foot, by land vehicles and by boat for the inspection of the preserving unities in Carajás, in 2020. As a result of that, 494 events were interrupted, involving illegal mining, predatory hunting and fishing, and invaders. Besides that, 424 items were seized, including fire guns, equipment for mining and ammunition.
Palavras-chave
COMPARTILHE ESSA NOTÍCIA